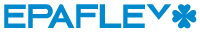
Epaflex Polyurethanes Spa - Società Unipersonale - Cap. Soc. € 1.000.000 i.v. - Sede legale: L.go Isabella d'Aragona 4, 20122 Milano.
Registro Imprese Milano 02144860968 - Rea Pavia 260624 - Rea Milano 1512571 - P.I. 11965210153 - C.F. 02144860968
• Excellent physical and mechanical properties
• Excellent resistance to oils, greases and many solvents
• Improved hydrolysis resistance
• Food approved grades
• Possibility of providing grades with tailored fluidity
• Wide range of hardness
• High elasticity and flexibility
• Good resistance to low temperatures
• Very good friction and scratch resistance
• Good tensile, tear and sheer strength
• Possibility of creating matt and glossy surfaces
• Very good welding capacity
• Recyclability
TPU is a hygroscopic polymer and the moisture absorbed affects its processability and the physical-mechanical properties
of the extruded/molulded articles.
The granules must be dried before use by using fan ovens, vacuum driers or dehumidifying air driers.
The percentage of moisture in the granule must be less than 0.05%.
Like TPU any masterbatches should also be dried separately from the TPU before being mixed. For the drying parameters
(time and temperature), please see our technical datasheets.
The exposure of TPU to the air for even just a few hours means moisture absorption and forces pre-drying once again.
Epaflex TPUs must be stored in a dry place at a room temperature preferably around 20° C and in any case not at a
too high or too low temperature preferably in a ventilated, cool room.
Epaflex TPUs come in various packaging such as: 25 kg aluminized bags and 600 kg. or 1000 kg. octabins.
Epaflex TPUs can be coloured with masterbatches.
Specific TPU-based masterbatches are recommended.
Like TPU, masterbatches should also be dried separately from the TPU before being mixed with it.
Processing waste and scraps can be re-used after having been re-granulated. In this case it is worth checking the absence of
impurities and ensuring that the product has not undergone heat degradation. The re-granulated product (like virgin TPU) should
always be dried before being re-used.
We suggest using re-granulated TPU blended with fresh granules at a percentage of no more than 25%.
For transforming our extrusion grade TPU we recommend the use of standard 3-stage single-screw extruders with “general
purpose” constant pitch screws (1 D) whose diameter is between 40 and 60 mm and L/D ratio between 20:1 and 30:1.
The compression ratio can range from 1:2 to 1:3.
In order to prevent the product from heat degradation the space between screw and cylinder must be between 0.1 and 0.2 mm
and the dies used must be designed so that there are no areas in which the material can stagnate.
We discourage the use of perforated disks and packets of filters.
Machines with a clamping pressure of no less than 150 tons and
injectors with three-stage screws of a diameter between 40 and
60 mm, and an L/D ratio between 20:1 and 30:1 are
recommended for injection moulding.
The use of screws with a diameter exceeding 65 mm and/or with
a high compression ratio is not recommended.
In order to avoid thermal degradation of the product (local
overheating of the material), it is essential to eliminate all the
possible points where stagnation may occur and check that the
nozzle is heated in a uniform manner for its whole length.
• Spiral Hoses
• Pneumatic Hoses
• Cable jacket
• Hydraulic tube jacket
• Profiles
• 3D filaments
• Conveyor belts
• Tooth belts
• Films
• Mechanical items
• Industrial components
• The mining industry
• Consumables
• Wheels, rollers
• Transmissions
• Transport
• Agriculture and gardening
• Automotive components
• 2K moulding
• Compound
Via Circonvallazione Est, 8, 27023 Cassolnovo PV, Italy
T. (+39) 0381929521
F. (+39) 0381929523
Epaflex Polyurethanes Spa - Società Unipersonale - Cap. Soc. € 1.000.000 i.v. - Sede legale: L.go Isabella d'Aragona 4, 20122 Milano.
Registro Imprese Milano 02144860968 - Rea Pavia 260624 - Rea Milano 1512571 - P.I. 11965210153 - C.F. 02144860968